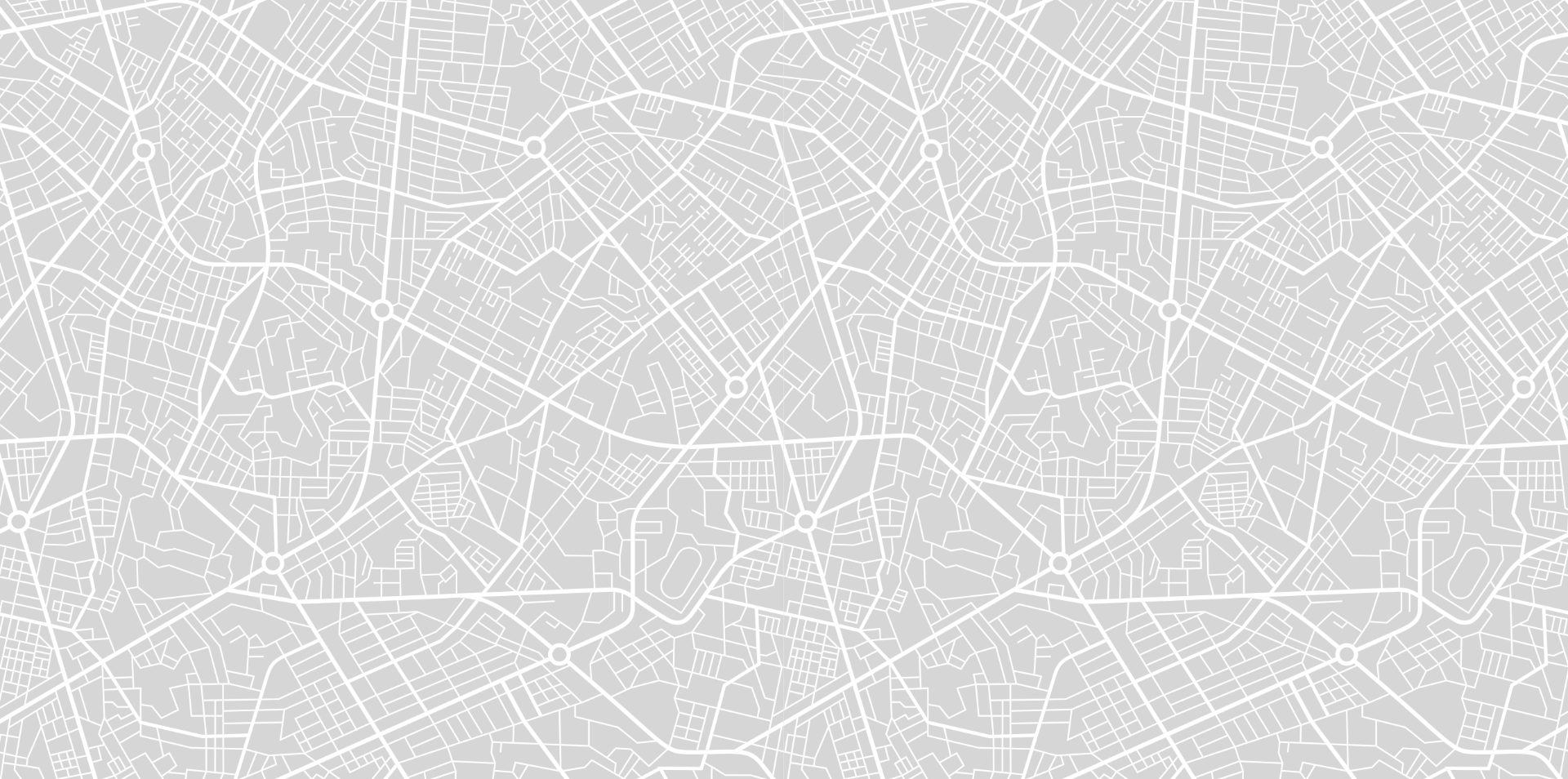
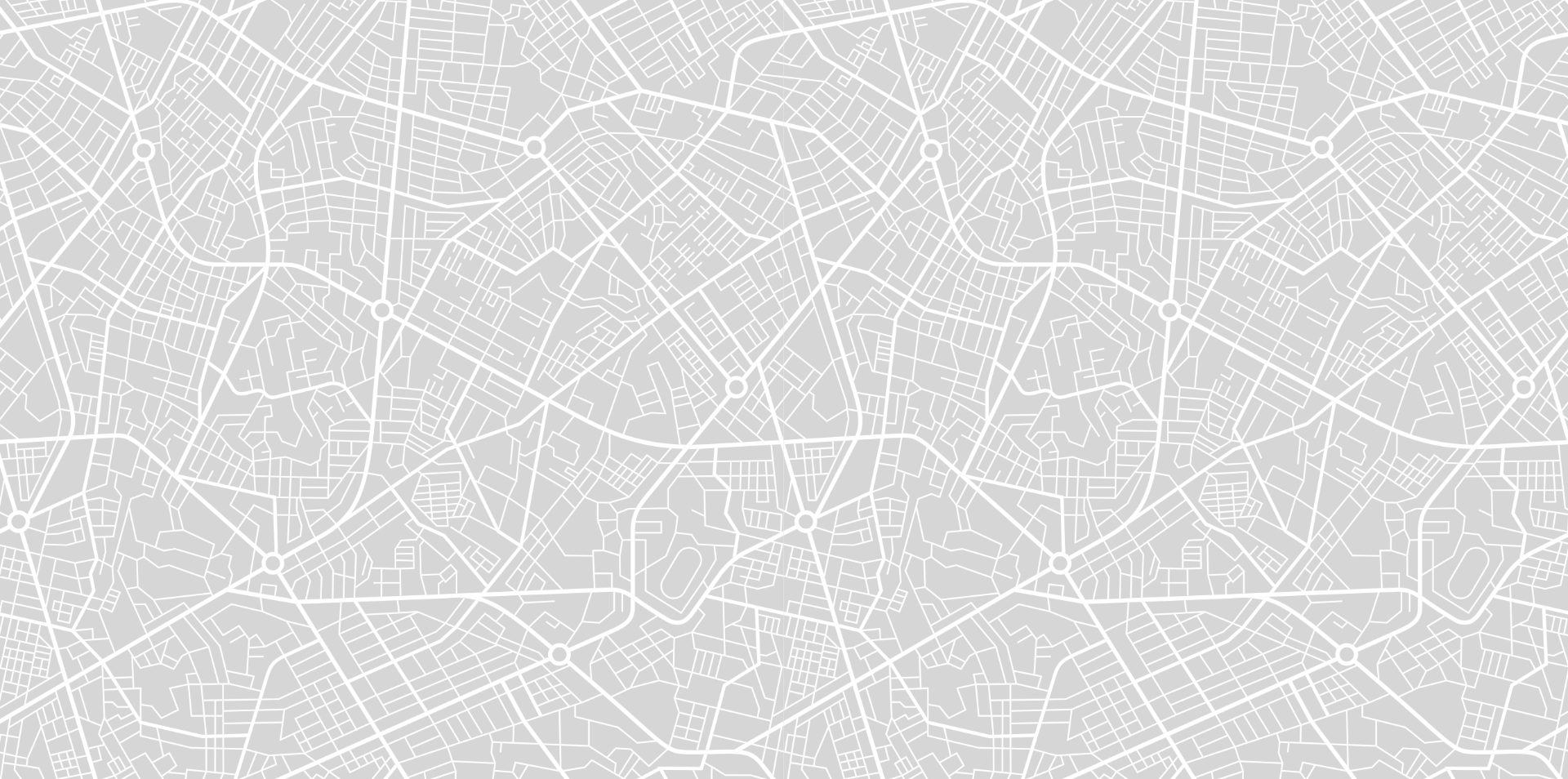
What is the definition of CNC automatic loading and unloading?
CNC (Computer Numerical Control) machines serve an important role in modern manufacturing, particularly in lathes, milling machines, and grinding machines. In typical manufacturing processes, CNC machining centers frequently encounter time-consuming issues when loading and unloading materials. Furthermore, as machines replace physical labor in material handling, placement issues come up. To overcome these difficulties, numerous novel techniques and technologies have been developed. But how can we know which loading and unloading systems are appropriate?
When determining a system, we can evaluate it according to the following aspects:
1. Type of objects loaded and unloaded
Different loading and unloading systems are appropriate for precision parts that require high positioning and clamping accuracy, as well as irregularly shaped, size-variable parts and difficult-to-handle heavy workpieces.
2. Processing procedure: frequency of material changes, and processing flow.
Does it necessitate high-precision machining or flexibility to changing processing flows? Is the processing flow predetermined, or does it necessitate large-scale motion processing?
Three popular automated loading and unloading methods
Robotic Arm with Six/Four Axis for Automatic Loading and Unloading
Several items can be handled by the robot arm-equipped independent loading and unloading system, particularly parts with complex shapes and high precision needs. Together using aids of vision, sensors, and fixtures, the system can precisely grasp, position, swiftly switch, and position objects if high precision and multiple types of processing are required. Because of its adaptability, it can change with the processing lines. It works particularly well in industrial settings where material changes are necessary on a regular basis as it can handle variations in showing up materials and maintain precision and stability during the gripping and setting operation.
Practical applications do have some restrictions, though. A number of variables, including the arm's length's operating range, load restrictions, and environmental factors, must be considered in production line design.
Precision Parts : Such as electronic components and precision mechanical parts that require high-precision gripping and placing.
Irregular Parts : Such as irregularly shaped plastic or aluminum products, requiring a flexible robotic arm and fixtures to adapt to different shapes and sizes.
Gantry Structure with Robotic Arm
Robotic arms with gantry designs can handle workpieces that need steady, wide-ranging movement and gripping because of their high load capabilities
They can also achieve relatively high precision, but the accuracy of the gripping position mainly depends on the mechanism's precision. Suitable for linear movement up and down as well as left and right, attention must be paid to the factory space layout and protective settings to ensure smooth processing lines.
Large Workpieces: Such as automotive parts and large mechanical parts that require stable, large-range movement and gripping.
Heavy Workpieces: Such as steel plates and metal frames, requiring a high-load capacity gantry-type robotic arm.
Workpiece Exchange System
Workpieces with set sizes and forms that don't require frequent material changes can be handled by workpiece exchange systems. These workpieces have modest accuracy requirements and are designed for simple material handling.
Processing lines are often straightforward and stationary, following a predetermined course and requiring few material changes on a regular basis.
This makes them ideal for settings with basic, fixed manufacturing lines.
Standard Parts : Such as standardized bolts and bearings with fixed shapes and sizes.
Repetitive Processing Parts : Such as mass production parts within molds, suitable for continuous production.
Comparison of Three Common Automated Loading and Unloading Methods
Feature | Six-Axis/Four-Axis Robotic Arm Automatic Loading and Unloading | Gantry Structure with Robotic Arm | Workpiece Exchange System |
---|---|---|---|
Suitable Workpiece Type | Precision parts, irregular parts | Large workpieces, heavy workpieces | Standard parts, repetitive processing parts |
Precision Requirements | High | Medium to High | Low |
Load Capacity | Medium | High | Medium |
Suitable Processing Line | Variable | Linear | Simple and Fixed |
Material Change Frequency | Frequent | Low | Low |
Notes | Consider arm length and load limitations | Consider factory space layout | Operates within a simple fixed path |
FAQ
Total Product Line and Expert Application Assessment by Ace Pillar
By choosing the right automated loading and unloading method, production efficiency and product quality are raised while labor costs and safety risks are reduced.
As the amount of automation in the component manufacturing industry increases, businesses must select the optimal automation solution based on specific requirements and application situations. This approach not only resolves current problems but also lays the foundation for future production line flexibility and customized production.
We hope that this information will help you make the best decisions regarding automated loading and unloading so that you may achieve continuous production optimization and greater competitiveness.